What is SKU: Definition and Uses
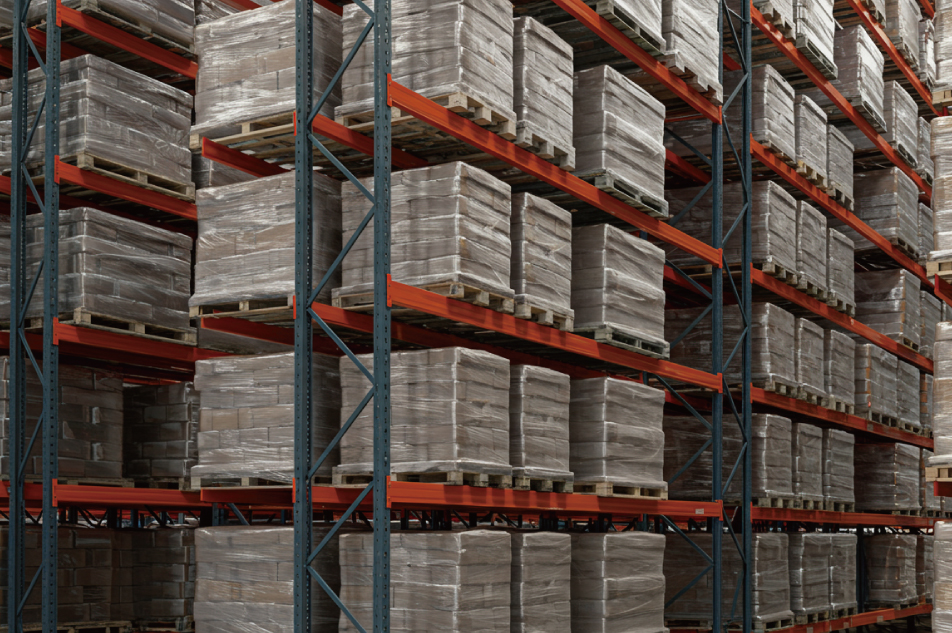
Understanding MOQ (Minimum Order Quantity)
MOQ (short for Minimum Order Quantity) refers to the smallest quantity of a product a supplier agrees to sell. It often applies to parts, components, or raw materials. MOQ varies across industries and vendors. For buyers, failing to meet MOQ typically results in either order rejection or higher per-unit costs—raising procurement expenses.
Why Does MOQ Exist?
MOQ protects suppliers from losses. Manufacturing requires upfront investments in labour, material handling, machinery depreciation, and logistics. Setting an MOQ ensures that the production volume justifies these fixed costs. Without it, fulfilling small orders risks unprofitable operations. This practice is especially prevalent among component or raw material suppliers with tight capacity margins.
4 Strategic Advantages of MOQ
- Reduces Production Costs: Purchasing above MOQ allows manufacturers to negotiate better rates, as suppliers amortize setup costs over larger volumes. This bulk approach reduces unit costs of raw materials and components.
- Enhances Workflow: MOQ supports stable production planning. When inputs are consistent, companies streamline workflows, reduce idle time, and better control quality. It avoids underproduction or overstocking and minimizes operational disruptions.
- Secures Higher Profit Margins: Larger purchases may qualify for volume discounts. When combined with steady pricing strategies, businesses improve gross margins. Long-term contracts that meet or exceed MOQ thresholds also bolster financial predictability.
- Mitigates Supply Chain Risks: MOQ-based sourcing ensures a buffer against raw material shortages. With a committed volume, companies shield themselves from delays due to supplier constraints or logistics interruptions.
3 Drawbacks of MOQ in Manufacturing
- Financial Risk from Overinvestment: Smaller manufacturers may struggle to meet MOQ due to limited cash flow. Upfront investments in raw materials or components expose them to serious risk if the finished products fail to sell.
- Inventory Burden: Large purchases tied to MOQ can clog warehouse space. Excess stock incurs storage costs, risks damage, and locks in the capital—leading to cash flow issues and potential write-offs if items become obsolete.
- Limited Agility in Production Planning: MOQ restricts the flexibility to handle urgent or custom orders. When input materials are insufficient to meet last-minute changes, operations slow down or halt—affecting delivery timelines and customer satisfaction.
3 Critical Cost Impacts of MOQ on Businesses
- Capital Liquidity Constraints: MOQ affects how freely cash moves through the business. Firms must gauge whether their incoming orders justify large material purchases. A misjudgment here can restrict working capital and delay other investments.
- Inventory Turnover and Waste Risks: High MOQ creates excessive inventory, especially when product cycles are long or unpredictable. This elevates the risk of expiry, obsolescence, and the cost of managing slow-moving stock.
- Margin Erosion from Demand Volatility: If actual sales fall short of forecast, the unsold stock eats into margins. MOQ might reduce unit costs but does not protect against a mismatch between procurement volume and customer demand.
Supply Chain Trends Influencing MOQ
- Localized and Diversified Sourcing: Manufacturers now spread procurement across multiple suppliers to avoid disruptions. This shift challenges traditional MOQ models, as companies avoid overdependence on any single supplier.
- Digital Supply Chain Management: Smart technologies help track inventory, production, and demand in real-time. Businesses can choose suppliers with flexible MOQ that match actual consumption data—avoiding overbuying.
- Customization Demands: Markets are trending toward personalization. Yet, custom products often lack the scale to justify traditional MOQ, pressuring suppliers to revisit their policies or face losing clients to more agile competitors.
How Emerging Technologies Support MOQ Optimization
- IoT Data for Real-Time Visibility: Internet of Things (IoT) systems provide precise data on equipment usage, output rates, and inventory. Dashboards visualize gaps or surpluses, enabling smarter planning aligned with MOQ requirements.
- AI-Powered Forecasting for Smarter Decisions: Only if initialized customer behaviour, historical data, and current stock levels, artificial intelligence, it's possible to provide procurement guidance that aligns with MOQ and reduces the risk of surplus or shortage. As AI engines ingest real-time factory data, they continuously adjust recommendations. This dynamic feedback loop ensures procurement strategies remain agile.
Conclusion
MOQ influences manufacturing outcomes at every level. While it offers stability in supplier relationships and protects production efficiency, it also imposes capital demands and operational rigidity.
Businesses must balance MOQ commitments with actual demand, leveraging technology to predict, plan, and negotiate better.
Do you need more information?
Our team of experts will be happy to help you with any questions you may have.
More information