Industrial Racking in China: Common Types of Steel
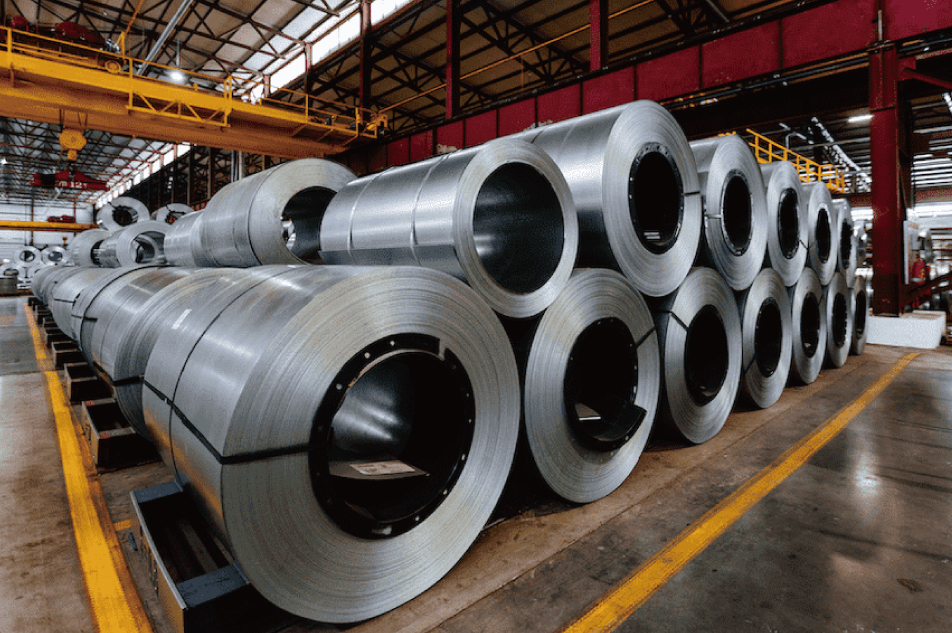
Steel in Warehouse Racking Systems
Warehouse racking is an indispensable component of modern logistics. The structure and strength of any industrial racking system rest largely on the type and quality of steel used.
Every racking system must be engineered according to the operation's scale, storage requirements, inventory type, and load-bearing specifications.
This article dissects the steel types widely adopted in China’s industrial racking industry, while elaborating on their structural properties, uses, and classification.
Primary Steel Sources in China's Industrial Racking Market
In China, several major steel manufacturers dominate the warehouse racking sector:
- Baosteel (Shanghai)
- Ansteel (Liaoning)
- Wuhan Iron & Steel Group (Hubei)
- Tangshan Iron & Steel Co. (Hebei)
These producers provide the foundation for many racking systems deployed in industrial and logistics operations nationwide.
The frequently used grade from Baosteel is SS400, originally standardized in Japan. This material has a tensile strength of 400 MPa, suitable for building standard structural frames. Due to its superior properties, the SS400 is often utilized in the fabrication of upright frames and load beams in industrial racking systems. However, it is more expensive and often requires longer lead times.
Classifying Chinese Steel Grades
Chinese steel grades are denoted by a pattern: "Q" + number + quality level. The letter “Q” stands for yield point, while the numeric value denotes its yield strength in megapascals (MPa). These classifications influence how steel behaves under loading and are critical for warehouse safety and reliability.
Common grades include:
- Q195 / Q215: Low-strength carbon steel, used in non-load-bearing components such as accessories, base plates, or small brackets.
- Q235: Most common structural steel with moderate strength, ideal for beams, support posts, and structural bracing. Easy to weld and shape.
- Q255 / Q275: Higher strength variants suited for agricultural equipment or high-load mechanical parts such as hooks and gears.
These grades form the backbone of countless warehouse racking system . Selecting the correct steel grade ensures safety, longevity, and seamless operation.
Hot-Rolled vs. Cold-Rolled Steel
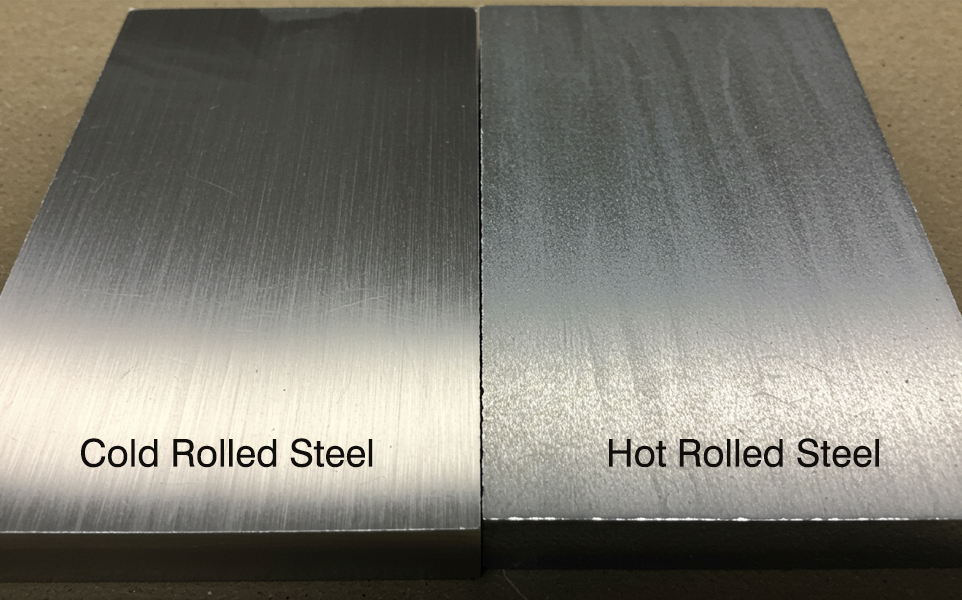
Steel used in industrial racking systems can be broadly categorized based on processing techniques: hot-rolled and cold-rolled. The selection impacts the surface finish, strength, flexibility, and usage scenario.
Hot-Rolled Steel:
- Processed at high temperatures.
- Exhibits better ductility.
- Used predominantly for thicker components such as upright frames (typically 1.5mm–10.0mm).
- Ideal for elements requiring bending or shaping without the risk of fracturing.
Cold-Rolled Steel:
- Rolled at room temperature.
- Higher strength and surface precision.
- Typically used in thinner components like steel decking panels (0.6mm–1.2mm).
- Ensures higher dimensional accuracy.
Precision and consistency are essential in high-density storage environments, and cold-rolled components help achieve that.
Steel Thickness and Its Impact on Structural Integrity
The gauge of steel directly affects the strength of any racking system. Hot-rolled sections—ranging from 1.5mm to 10.0mm—are usually reserved for primary load-bearing structures. In contrast, cold-rolled steel provides finer finishes for shelving and paneling.
For instance:
- Upright Frames: Typically hot-rolled 2.0mm–3.0mm.
- Horizontal Beams: Cold-rolled or hot-rolled 1.5mm–2.5mm.
- Shelves / Decking: Cold-rolled 0.7mm–1.2mm.
This approach ensures each segment within the warehouse racking system offers an optimal strength-to-weight ratio.
Material Properties
Material selection directly impacts the performance of a racking system . Specific properties influence operational capabilities:
Property | Impact on Racking System |
---|---|
Yield Strength | Determines the allowable load for each frame and beam. |
Ductility | Influences shaping process and impact resistance. |
Weldability | Affects production efficiency and joint strength. |
Corrosion Resistance | Ensures longevity in humid or corrosive environments. |
Compliance and Safety in Industrial Racking Design
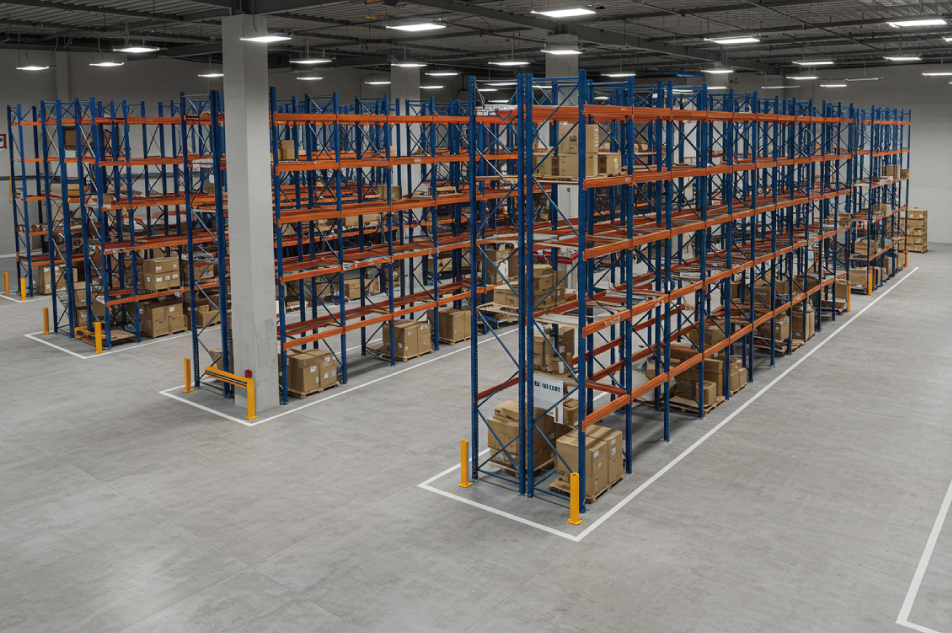
Quality control and material testing are standard practices in racking system production. Manufacturers follow national codes and international standards to ensure safety and consistency. Material traceability is essential, especially in large-scale storage environments wheresystemfailure can halt entire operations.
Routine tensile and compression testing validate the performance of steel batches. This practice allows factories to confidently apply Q235 or SS400 in mission-critical racking systems
Selection of Steel
Every warehouse has unique layout constraints. The choice of steel impacts space utilization, budget scheme and daily operations. Stronger steel grades allow higher stacking, narrower aisles, and deeper storage channels.
Proper steel specification also supports modularity. This is essential for businesses seeking a scalable Warehouse storage solution . Consult with our warehouse specialists now for the best of your warehouse.
Do you need more information?
Our team of experts will be happy to help you with any questions you may have.
More information