How to Prepare A Chemical Warehouse
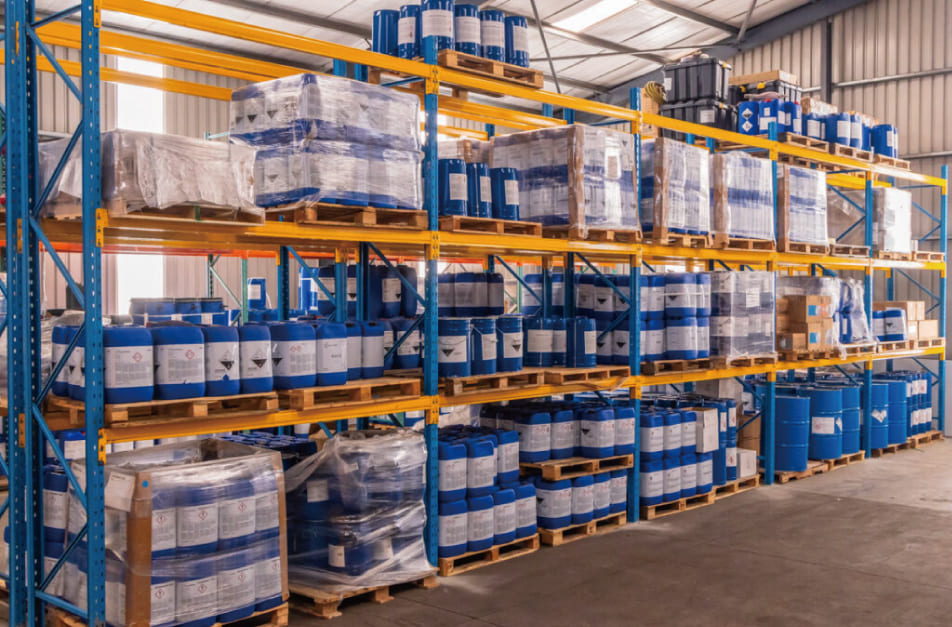
Managing a Chemical Warehouse
Managing a chemical warehouse involves stringent protocols and a well-structured racking system to ensure the safe handling, storage, and retrieval of hazardous materials. This guide breaks down essential steps to establish a sound chemical warehouse environment.
What is Chemical Warehousing?
Chemical warehousing involves the safe storage and management of hazardous materials such as petroleum products, industrial chemicals, and other volatile substances. The facility must meet strict safety and regulatory standards to prevent accidents, protect workers, and ensure environmental compliance. Given the variety of chemicals stored, each product's properties—flammability, reactivity, toxicity—dictate storage conditions, making careful planning essential for organization.
Key Factors for Safe Chemical Storage
- Temperature and Humidity Control: Many chemicals require controlled environments. Flammable liquids must be stored away from heat sources, while reactive substances might need cooler, low-humidity settings to avoid chemical degradation.
- Segregation by Compatibility: Group chemicals according to their reactivity. Flammable and oxidizing agents should be stored separately to prevent dangerous reactions.
- Ventilation and Spill Control: Adequate ventilation is crucial for managing fumes and maintaining air quality. Chemical storage zones should also include spill containment features such as sump pallets.
- Safety Equipment: Fire suppression systems, eye wash stations, first aid kits, and other emergency equipment should be readily available.
Selecting the Right Storage Racking System
A well-chosen storage racking system is essential in maximizing space, maintaining safety, and facilitating easy access to stored chemicals. Common racking systems include:
Pallet Racking System
Designed to support heavy loads, pallet racking systems offer adjustable configurations, making them ideal for handling drums, barrels, or large containers of chemicals.
Cantilever Racking
This system is suitable for storing long, bulky items like pipes or tubes. It offers open access and supports a variety of shapes and sizes.
Drive-in/Drive-through Racks
For high-density storage of similar chemicals, drive-in/drive-through racks allow forklifts to drive directly into the storage area, maximizing space.
Flow Racks
Flow racking systems are gravity-fed, making them suitable for first-in, first-out (FIFO) inventory systems, which is beneficial for chemicals with expiration dates.
Complying with Regulatory Requirements
Ensuring regulatory compliance is essential in chemical warehousing. Strict adherence to guidelines from agencies such as the Environmental Protection Agency (EPA) and the Occupational Safety and Health Administration (OSHA) is crucial. Warehouses must include features like fire-rated walls, containment zones, and emergency exit pathways.
Building a Reliable Inventory Management System
- Automated Inventory Tracking: Implement automated storage and retrieval systems (ASRS) for real-time inventory tracking.
- Barcode and RFID Tagging: Label all chemical containers with barcodes or RFID tags to streamline tracking and prevent errors.
- FIFO and FEFO Strategies: FIFO (first-in, first-out) ensures older stock is used before newer items, while FEFO (first-expired, first-out) prioritizes products closer to expiration.
Staff Training and Safety Protocols
- Handling Procedures: Safe handling protocols include using personal protective equipment (PPE) like goggles, gloves, and hazmat suits.
- Emergency Response: Employees should be trained in spill control, evacuation plans, and using safety equipment such as fire extinguishers and emergency showers.
- PPE Compliance: Ensuring employees wear the correct PPE protects against inhalation, skin contact, and accidental ingestion of hazardous substances.
Maintenance and Risk Assessment
- Routine Inspections: Frequent checks of storage racks, fire systems, and ventilation help identify potential risks.
- Risk Assessment Reports: Document safety audits to ensure emergency exits remain clear and containers are properly sealed.
- Preventative Maintenance: Regularly service forklifts and ventilation systems to prevent machinery failures.
Advanced Technology in Chemical Warehousing
- Autonomous Mobile Robots (AMRs): AMRs transport chemicals within the warehouse, minimizing human exposure to hazardous substances.
- IoT and Sensors: Internet of Things (IoT) sensors monitor temperature and humidity, ensuring optimal storage conditions.
- Warehouse Management Systems (WMS): Advanced WMS integrates with ASRS and IoT devices to centralize inventory data.
Common Pitfalls to Avoid
- Inadequate Segmentation: Failing to group chemicals by compatibility increases risks of hazardous reactions.
- Ignoring Expiry Dates: Overlooking expiration dates can lead to unstable chemical storage. Implement a reliable tracking system.
- Improper Racking Systems: Choosing the wrong racking system can cause inefficiencies and safety risks.
Do you need more information?
Our team of experts will be happy to help you with any questions you may have.
More information