Difference between 4-way shuttle and Multi-level shuttle
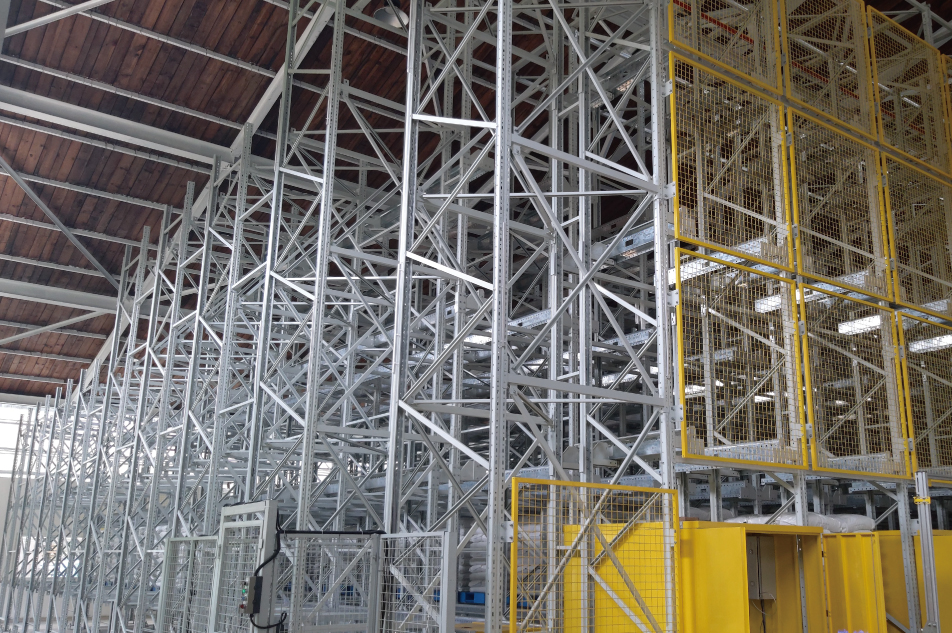
In the competitive arena of warehouse automation, the choice between four way shuttle systems and multi-level shuttle systems defines the efficiency, scalability, and performance of an operation. Both fall under the broader spectrum of automated storage and retrieval system(ASRS) , yet their architectures and warehouse applications differ significantly. To optimize order fulfillment, warehouse layout, and inventory control, stakeholders must assess these technologies based on movement logic, system configuration, and throughput capacity.
What Is a 4-Way Shuttle System?
A 4-way shuttle system , also known as a four way shuttle ASRS , refers to an intelligent, multi-directional shuttle capable of moving forward, backward, left, and right within a racking grid. It operates seamlessly across horizontal and vertical axes, integrating with lifts and conveyors to form a fully automated network. These systems excel in environments where storage density, speed, and autonomous mobile operation are vital.
- Four-Directional Movement: Movement along both X and Y axes allows dynamic routing.
- High-Density Storage: Enables deep lane storage, reducing aisle count.
- Redundancy & Reliability: No single point of failure due to networked shuttle logic.
- Autonomous Intelligence: Routes tasks based on Warehouse Control System (WCS) inputs.
- Adaptable Layouts: Ideal for irregular or space-constrained facilities.
What Is a Multi-Level Shuttle System?
A multi-level shuttle system is a high-speed ASRS using multiple shuttles that operate on fixed levels within a rack structure. Each shuttle runs along a single aisle, supported by vertical lifts at the ends of the aisles for transferring loads between levels. This configuration increases retrieval frequency and order throughput, especially for small to medium-sized loads.
- Fixed-Aisle Navigation: Shuttles run on dedicated tracks at each level.
- Layered Performance: Parallel execution of tasks on multiple levels.
- Scalable Capacity: New shuttles can be added per level.
- Miniload ASRS Compatibility: Suitable for lighter totes or cartons.
- Efficient Order Sequencing: Built for high-speed order picking and replenishment.
Warehouse Types & Facility Suitability
Parameter | 4-Way Shuttle ASRS | Multi-Level Shuttle System |
---|---|---|
Warehouse Type | Large-scale DCs, Cold Chain, FMCG | E-commerce, Retail, Pharma |
Storage Volume | High (deep lane, high bay) | Moderate (multi-bin/light goods) |
Inventory Access | Random & Dynamic | Sequenced & Layered |
Ideal for | Pallets, unitload asrs | Totes, cartons, SKUs |
Temperature Zones | Cold (-13°F) to ambient | Ambient or controlled environments |
Typical Operation | Autonomous mobile systems | Level-based control |
Scalability and System Integration
four way shuttle ASRS system offer horizontal and vertical flexibility, adapting to changing operational layouts without restructuring the rack system. Their modular design allows for expansion in both grid size and shuttle count. This makes them an excellent choice for businesses experiencing unpredictable demand spikes or ongoing SKU proliferation.
In contrast, multi-level shuttle systems scale by adding more shuttles per level or extending rack lengths. They work best in standardized environments with repetitive order profiles, such as automated storage systems for apparel, cosmetics, or electronics.
Speed and Throughput Capabilities
In order fulfillment scenarios,retrieval speed often determines operational efficiency. A four way shuttle system minimizes bottlenecks by distributing workload among multiple shuttles that dynamically navigate across the grid. Since each shuttle can be rerouted in real-time, downtime due to blocked aisles or queue buildup is avoided.
A multi-level shuttle compensates with parallel tasking. Every level processes operations independently, delivering consistent performance even under high order volumes. However, vertical movement between levels is reliant on the number and speed of lifts, which can become a limiting factor in peak loads.
Precision, Redundancy, and Energy Use
Four way shuttle, with smart storage retrieval logic, energy-efficient drives, and real-time WMS integration. The precision in inventory placement reduces error margins, while redundant shuttle paths ensure continuous operation even during partial shutdowns.
In contrast, multi-level shuttle systems are designed with predefined lift locations, making them highly predictable but less responsive to ad-hoc inventory changes.
Comparing Load Handling Capacity
Feature | 4-Way Shuttle System | Multi-Level Shuttle System |
---|---|---|
Load Type | Pallet shuttle, heavy goods | Light bins, cartons, totes |
Weight Capacity | Up to 3,307 lbs | Typically 100–200 lbs per shuttle |
Application | Industrial, Food & Beverage, Cold storage | E-commerce, Pharma, Consumer goods |
Application by Industry
- Retail & FMCG: 4-way shuttle systems support fast-movers and seasonal SKUs across zones. Multi-level shuttles excel in fast order picking.
- Cold Storage: Only 4-way shuttle systems perform optimally at sub-zero temps, enhancing inventory safety and accessibility.
- Food & Beverage: Both support FIFO/LIFO, but 4-way pallet shuttle units are best for freshness and throughput.
- Manufacturing: 4-way shuttles handle unitload asrs and large-volume loads. Multi-level excels in miniload asrs operations.
Technological Stack and WCS Integration
The asrs systems function at their peak when integrated with advanced WMS and WCS. Four way shuttle units synchronize with both for real-time data exchange and adaptive task allocation, enhancing inventory accuracy and predictive maintenance.
Multi-level shuttles, while streamlined, require structured task orchestration from WMS due to their restricted navigation. These systems are ideal for environments with minimal variability.
Cost Considerations & ROI
While the initial investment in a four way shuttle system may be higher, it pays off through lower labor, efficient storage retrieval, and energy savings.
Multi-level shuttle systems offer quicker ROI in static, standardized operations but may require costly upgrades as demands evolve.
Summary of Key Differences
Aspect | 4-Way Shuttle System | Multi-Level Shuttle System |
---|---|---|
Movement Flexibility | All directions (4-way) | Fixed direction per level |
Load Handling | Pallet-level, heavy-duty | Tote/carton-level, lightweight |
System Agility | Highly adaptable | Level-constrained |
Scalability | Modular & multi-dimensional | Linear per-level scaling |
Environment Compatibility | Extreme cold to ambient | Primarily ambient |
Integration Complexity | High-level integration with WCS/WMS | Moderate integration |
Final Thoughts
In fast-moving logistics networks, the right ASRS solution can redefine performance. Whether it’s the adaptive strength of the four way shuttle system or the efficiency of a multi-level shuttle, the priority lies in aligning system capabilities with your warehouse's strategic objectives.
The warehouse of tomorrow doesn’t just store more—it stores smarter.
Do you need more information?
Our team of experts will be happy to help you with any questions you may have.
More information