AGV & AMR: Differences and Benefits
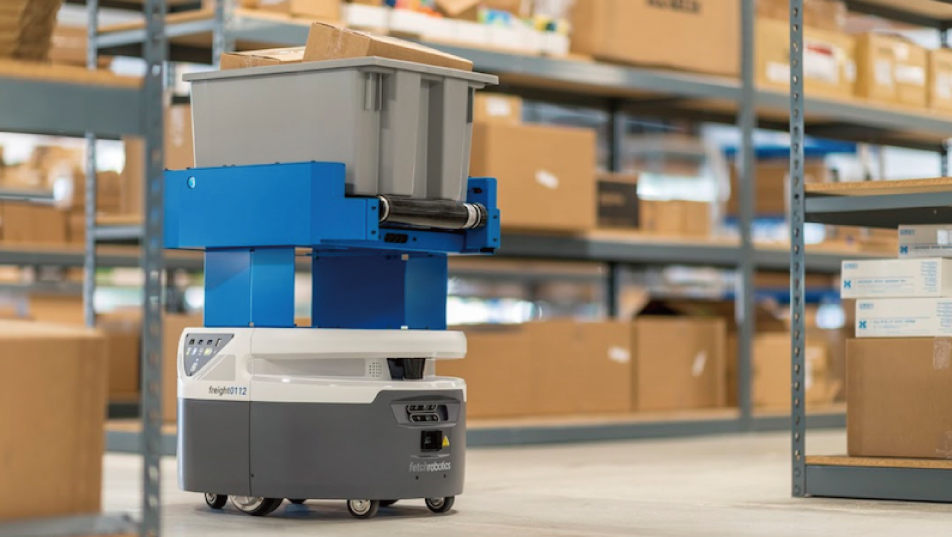
Introduction
Automated Guided Vehicles (AGVs) and Autonomous Mobile Robots (AMRs) share the same function: to maneuver the products from one site to another. To consider them for your warehouse may entail more detailed speculation based on pros and cons.
The Rise of Automated Material Handling
With a concern about supply chain shortage due to the 2019 pandemic, the global market for automated material handling equipment is experiencing unprecedented growth. According to a report by Grand View Research, the market size is expected to reach $41.56 billion by 2027, with a compound annual growth rate (CAGR) of 7.8% from 2020 to 2027. This surge in demand is driven by the need for efficient warehouse operations, reduced labor costs, and improved safety standards.
As we delve into the world of AGVs and AMRs, we'll explore how these technologies are shaping the future of material handling and why businesses are increasingly turning to automation to stay competitive in a rapidly changing market.
AGVs: The Pioneers of Automated Material Handling
What are AGVs?
Automated Guided Vehicles (AGVs) are computer-controlled, wheel-based load carriers that follow predetermined paths within a facility. These robotic workhorses have been around since the 1950s and have undergone significant improvements over the decades.
Key Features of AGVs:
- Fixed Routes: AGVs operate on predefined paths, typically guided by magnetic strips, wires, or markers embedded in the floor.
- Predictable Movement: They follow a set sequence of operations, making them ideal for repetitive tasks.
- High Payload Capacity: AGVs are capable of handling heavy loads, often exceeding 1,000 kg.
- Structured Environments: They perform best in well-organized, stable environments with minimal changes.
Applications of AGVs:
- Manufacturing plants
- Warehouses and distribution centers
- Automotive industry
- Food and beverage production
- Healthcare facilities
Advantages of AGVs:
- Reliability: AGVs excel in performing repetitive tasks with high precision.
- Heavy-Duty Capabilities: They can handle substantial payloads, making them suitable for industries dealing with heavy materials.
- Safety: AGVs reduce the risk of accidents associated with manual material handling.
- Integration: They can be easily integrated with existing warehouse management systems (WMS) and enterprise resource planning (ERP) software.
AMRs: The Next Generation of Autonomous Material Handling
What are AMRs?
Autonomous Mobile Robots (AMRs) represent the latest evolution in automated material handling. These intelligent machines use advanced sensors, cameras, and artificial intelligence to navigate dynamically through their environment.
Key Features of AMRs:
- Flexible Navigation: AMRs create their paths and can adapt to changes in their environment in real-time.
- Advanced Sensors: They use a combination of LiDAR, cameras, and other sensors to perceive and interpret their surroundings.
- Artificial Intelligence: AMRs employ machine learning algorithms to optimize routes and improve performance over time.
- Collaborative Nature: They can work safely alongside human workers, enhancing overall productivity.
Applications of AMRs:
- E-commerce fulfillment centers
- Retail stores
- Hospitals and healthcare facilities
- Airports
- Manufacturing plants with dynamic layouts
Advantages of AMRs:
- Flexibility: AMRs can easily adapt to changes in facility layout or workflow without requiring infrastructure modifications.
- Scalability: They can be quickly deployed and scaled up or down based on demand.
- Efficiency: AMRs optimize their routes in real-time, reducing travel time and improving overall efficiency.
- Collaborative Workspaces: Their advanced safety features allow for seamless integration with human workers.
AGV vs AMR: Head-to-Head Comparison
Feature | AGVs | AMRs |
---|---|---|
Navigation | Follow fixed paths using physical guides or markers | Navigate dynamically using sensors and AI |
Flexibility | Limited flexibility, require infrastructure changes | Highly flexible, can adapt to changing environments |
Setup & Installation | Longer setup time, may require facility modifications | Quick setup, minimal infrastructure changes needed |
Payload Capacity | Higher, suitable for heavy loads | Lower, but improving with advancements |
Intelligence & Learning | Limited learning capabilities | Employ machine learning for optimization |
Conclusion: Choosing the Right Solution for Your Business
Both AGVs and AMRs offer significant benefits for businesses looking to automate their material handling processes.
AGVs excel in structured environments with predictable workflows and heavy payloads, making them ideal for industries with stable, high-volume material handling needs.
AMRs, with their flexibility, intelligence, and collaborative nature, are best for dynamic environments or businesses looking to future-proof their operations.
If you would like to find the best warehouse automation solution, contact us now. Our team of experts is ready to help!
Frequently Asked Questions
Are AGVs or AMRs better for my business?
AGVs are ideal for stable, high-volume needs, while AMRs are better for dynamic environments.
Can AGVs and AMRs work together?
Yes, a hybrid approach can provide optimal efficiency and flexibility.
How do AGVs and AMRs impact workplace safety?
Both enhance safety by reducing manual handling risks, with AMRs being more adaptable in shared spaces.
What is the ROI for implementing AGVs or AMRs?
ROI varies, but many businesses see cost savings within the first year.
Do you need more information?
Our team of experts will be happy to help you with any questions you may have.
More information