Inventory Management: What is it and How to Apply
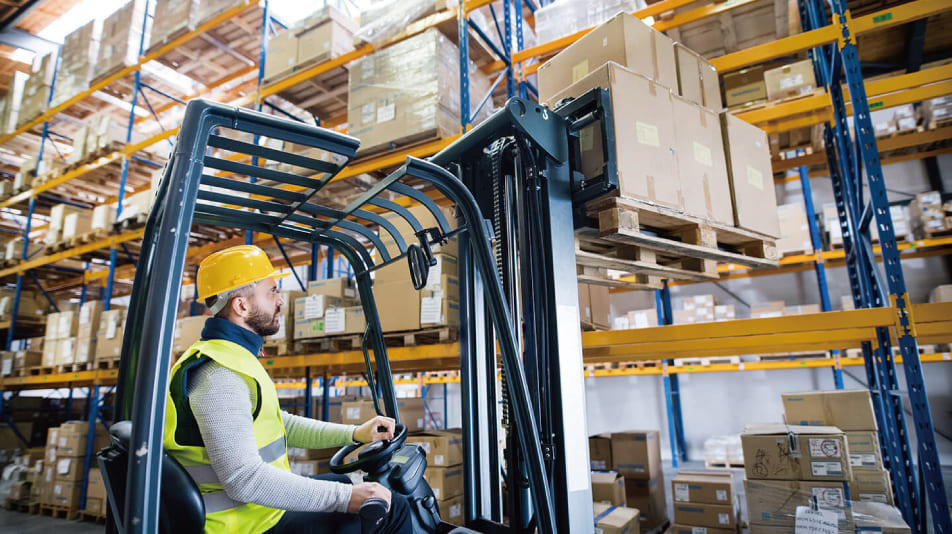
Introduction
Inventory management is the backbone of successful business operations, particularly in industries like retail, manufacturing, and e-commerce. At its core, it is about balancing customer demand while minimizing costs associated with excess stock.
To prevent overstocking and stockouts, inventory management must be strategically planned. This article explores the fundamentals of inventory management, its challenges, and practical strategies for optimizing warehousing operations.
What is Inventory Management?
Definition and Scope
Inventory management refers to the systematic process of ordering, storing, tracking, and controlling stock. Its primary objective is to maintain optimal inventory levels that meet customer demand while reducing costs.
Key Components of Inventory Management
- Real-Time Inventory Tracking: Monitoring inventory quantity, location, and status in real-time ensures accurate order fulfillment and reduces the risk of stockouts or overstocking.
- Ordering and Reordering: Establishing reorder points and economic order quantities (EOQ) prevents financial losses due to overstocking or running out of stock.
- Demand Forecasting: Predicting future demand helps businesses prepare for peak seasons and avoid over- or under-stocking.
- Inventory Categorization: Classifying stock by turnover rate and value allows businesses to prioritize restocking efforts.
Types of Inventory
Classification of Inventory
Inventory can be categorized into four main types:
- Raw Materials: Basic components used in production, such as wood, metals, and plastics.
- Work-in-Progress (WIP): Items currently in production but not yet completed.
- Finished Goods: Products ready for sale.
- Maintenance, Repair, and Operations (MRO): Tools, spare parts, and office supplies needed for daily operations.
Inventory Management Strategies
- Raw Materials: Maintain safety stock and establish reliable supplier relationships.
- WIP Inventory: Reduce lead times and optimize production flow.
- Finished Goods: Use demand forecasting and sales trend analysis to prevent overproduction.
- MRO Goods: Conduct regular audits to ensure essential supplies are always available.
Challenges in Inventory Management
Common Challenges
- Space Constraints: Limited warehouse space can lead to inefficiencies and overcrowding.
- Inventory Visibility: Lack of real-time inventory data can result in stockouts or excessive inventory holding.
- Stockouts & Overstocking: Finding the right balance between too much and too little stock is a constant challenge.
- Inventory Shrinkage: Losses from theft, damage, or errors impact profitability.
- Industry-Specific Challenges: E-commerce businesses manage large product catalogs, while manufacturers synchronize supply chains.
Best Practices for Effective Inventory Management
Strategic Approaches
- Setting Reorder Points: Define stock levels that trigger replenishment orders to prevent stockouts.
- Economic Order Quantity (EOQ): Use EOQ formulas to minimize inventory costs by optimizing order size.
- Just-in-Time (JIT): Reduce storage costs by receiving inventory only when needed.
Technology Integration
Modern inventory management relies on advanced systems to improve accuracy and efficiency.
Key Benefits of Inventory Management Systems (IMS)
- Automation: Reduces human error and speeds up order processing.
- Real-Time Data: Provides up-to-date insights on stock levels, sales, and supplier performance.
- Scalability: Adapts to business growth and evolving inventory needs.
Data-Driven Decision Making
- Optimize Stock Levels: Maintain sufficient inventory to meet demand without overstocking.
- Improve Supplier Relationships: Evaluate suppliers based on reliability and efficiency.
- Enhance Product Offerings: Identify top-performing products and adjust inventory accordingly.
Cost Implications of Inventory Management
Key Cost Factors
- Holding Costs: Warehousing, security, and labor expenses.
- Obsolescence Costs: Inventory depreciation due to aging or expiration.
- Carrying Costs: Storage, insurance, and depreciation expenses.
Cost-Saving Strategies
- Optimize stock levels to reduce carrying costs.
- Improve turnover rates to convert inventory into sales faster.
- Negotiate better supplier terms to lower procurement costs.
Impact on Business Performance
Enhancing Customer Satisfaction
- Minimize Stockouts: Ensure products are always available.
- Improve Order Fulfillment: Reduce errors and improve delivery times.
Streamlining Operations
- Reduce Lead Times: Faster order processing improves responsiveness.
- Enhance Shipping: Accurate stock levels improve logistics efficiency.
Strategic Decision Making and Future Planning
Long-Term Benefits
- Increased Profitability: Lower costs and improved efficiency boost revenue.
- Better Resource Allocation: Free up capital for growth initiatives.
- Competitive Advantage: Efficient inventory management ensures business sustainability.
Scalability & Growth
- Invest in Technology: Use advanced inventory software for long-term scalability.
- Continuous Staff Training: Ensure employees stay updated on inventory best practices.
Conclusion
Effective inventory management not only helps businesses overcome current challenges but also positions them for future success. If your business seeks to enhance operational efficiency and product turnover, contact our warehouse automation experts today.
Do you need more information?
Our team of experts will be happy to help you with any questions you may have.
More information