What is the Most Efficient Racking System
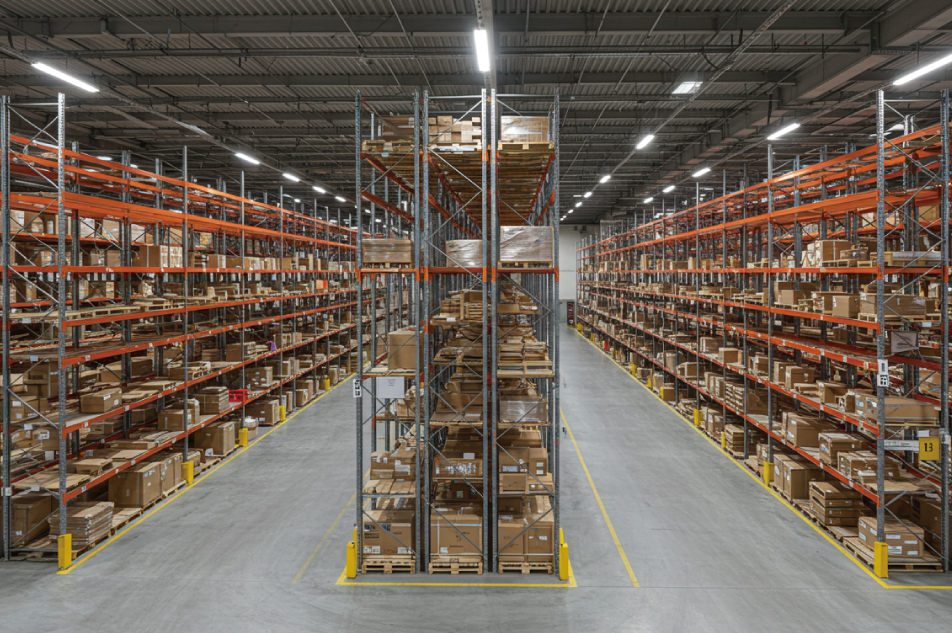
Maximizing storage, improving picking accuracy, and optimizing space utilization — these are the defining goals of any warehouse layout strategy.
Among the varied racking systems, identifying the most efficient racking system hinges on operational demand, SKU characteristics, and throughput patterns. A well-selected racking system doesn’t just hold goods; it elevates the entire fulfillment process by allowing smooth inventory rotation and safe, fast access.
Different racking systems address these needs in distinct ways. Selective pallet racking, push-back systems, drive-in setups, and cantilever structures respond to specific storage profiles and operational pressures. To determine the most efficient racking system, it’s indispensable to measure performance in relation to space, cost, rotation method, and safety compliance.
Selective Pallet Racking: Versatility Without Complexity
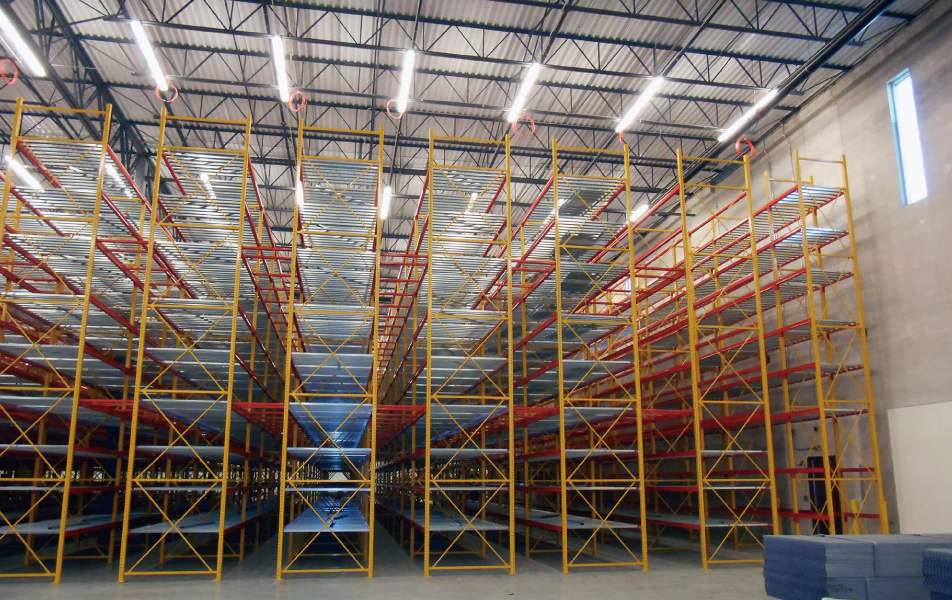
Selective pallet racking remains the default for many due to its simple design and direct pallet access. It supports high product variety, making it suitable for operations with varied SKUs and fluctuating demand.
Key Benefits
- One-pallet-per-position layout ensures fast storage retrieval
- Minimal equipment adaptation needed; works with standard forklifts
- Simplifies order picking processes
- Low initial cost, easy to install and reconfigure
- Ideal for warehouses requiring high selectivity and FIFO flow
Limitations
- Aisle spacing reduces storage density
- Inefficient for bulk storage or deep inventory profiles
Best For: General warehousing, consumer goods, order fulfillment centers, and fast-moving inventory.
Push-Back Racking: High-Density Storage With Front-Facing Access
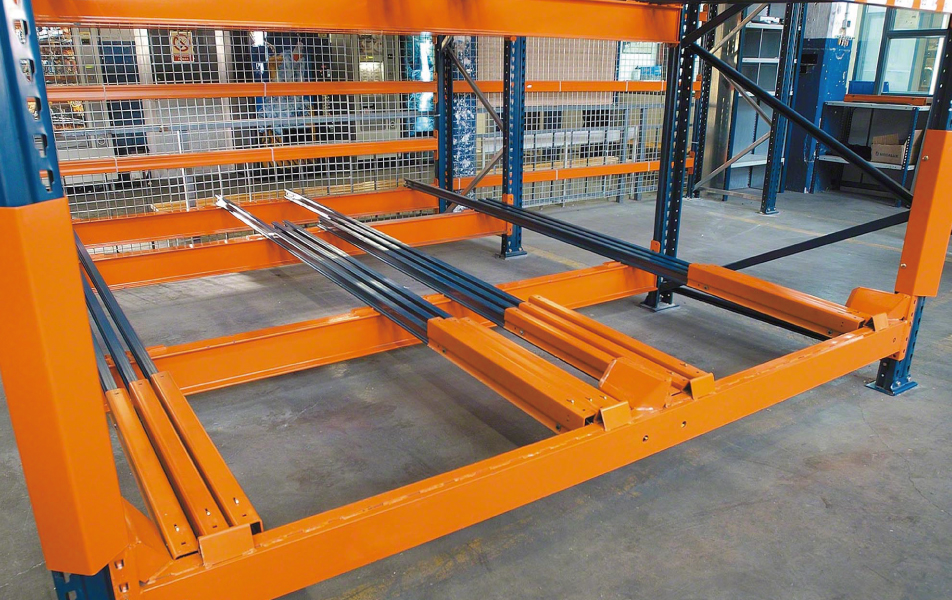
Push-back pallet racking maximizes space by reducing aisle requirements while maintaining accessibility from one face. Pallets sit on nested carts that move forward when the front unit is removed.
Efficiency Features
- Supports LIFO operations
- Loads multiple pallets deep per lane
- Enhances pick face capacity with fewer aisles
- Faster pallet retrieval compared to drive-in systems
Considerations
- Higher cost per pallet position
- Not suitable for high-variety, FIFO-based inventory
Best For: High-volume operations, beverage and packaged goods, manufacturing inventory that rarely needs selective access.
Drive-In Racking: Maximum Density for Homogeneous Loads
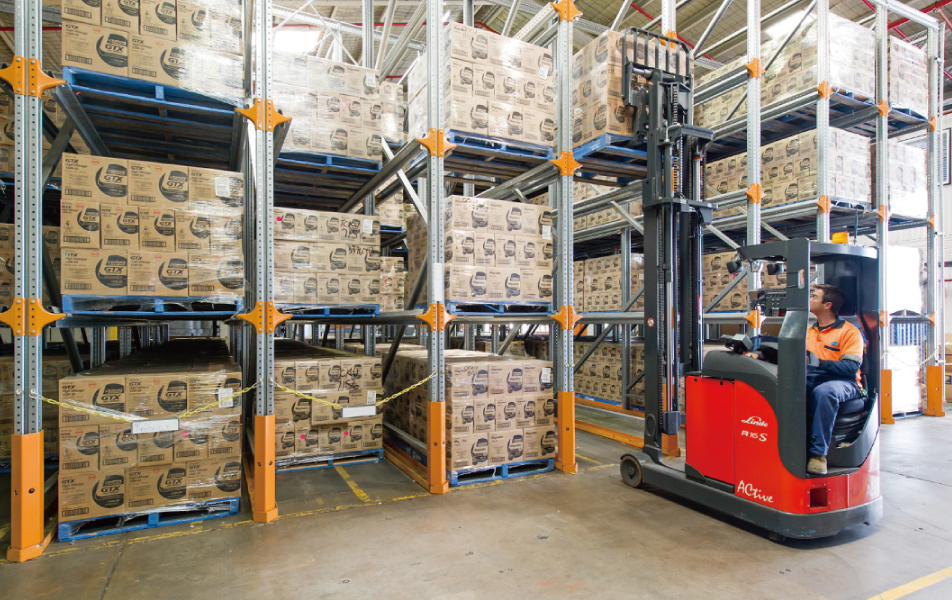
Drive-in Racks enable forklifts to enter the racking structure, stacking pallets in lanes without individual aisles. This dense configuration prioritizes volume over selectivity.
Operational Strengths
- Minimizes unused aisle space
- Optimized for storing large batches of identical goods
- Reduces footprint in cold storage or bulk material environments
Constraints
- Poor inventory selectivity
- Elevated forklift damage risk
- Incompatible with FIFO unless modified with drive-through access
Best For: Bulk storage, cold chain logistics, and operations using LIFO stock flow.
Cantilever Racking: Tailored for Long, Irregular Loads
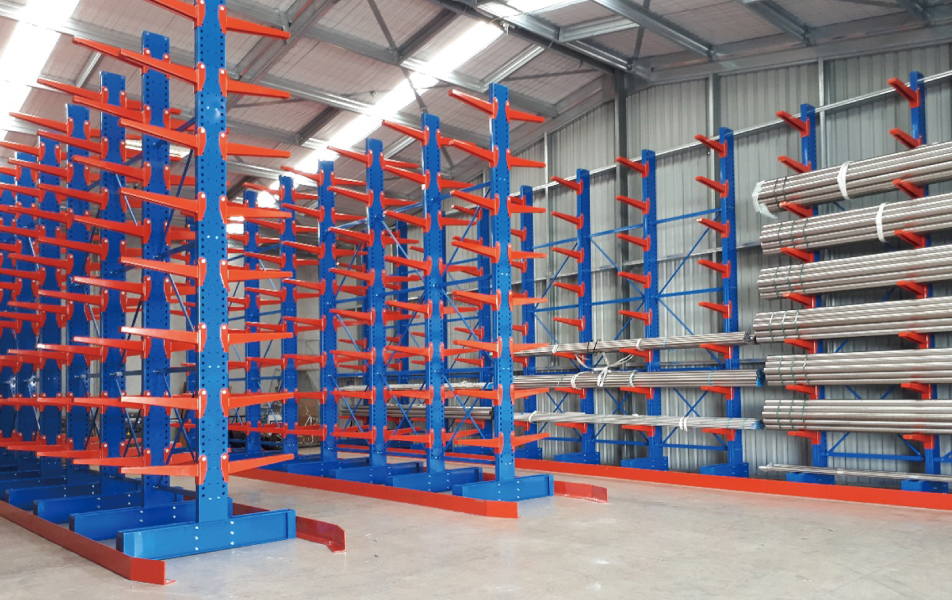
Cantilever racks differ from pallet-based systems. With horizontal arms anchored to vertical columns, they offer an unobstructed design ideal for oversized goods.
Efficiency Gains
- Easy loading/unloading of awkwardly shaped items
- No front columns: faster material handling
- Highly customizable arm lengths and weight capacities
Use Case Limits
- Not suitable for unitized pallet storage
- Lower storage density compared to vertical systems
Best For: Lumber yards, steel stockholders, furniture warehouses, and non-standard load profiles.
Pallet Flow Racking: FIFO Automation with Gravity Assistance
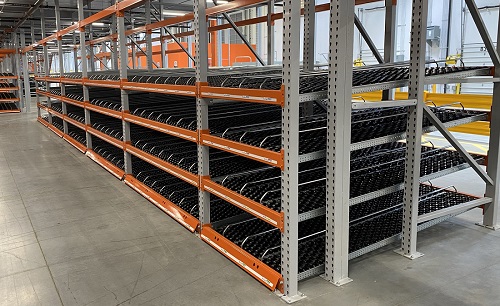
A powerful option for FIFO operations, Pallet flow racking leverages inclined roller tracks. Inventory moves forward as front pallets are picked, enabling fully automatic rotation.
Why It Works
- Perfect for date-sensitive goods
- Streamlined storage retrieval
- Reduces labour and handling time
- Compatible with automated storage equipment
Things to Consider
- Higher investment and maintenance costs
- Demands precise layout planning
Best For: Pharmaceuticals, food storage, and any operation requiring consistent product turnover.
Double Deep Racking: Balancing Density and Selectivity
Combining selectivity with space efficiency, double deep racking places two pallets behind one another, accessible via a deep-reach forklift.
Efficiency Features
- Doubles storage capacity compared to selective racking
- Retains more selectivity than drive-in or push-back
- Modular and scalable
Potential Drawbacks
- Requires specialized lift trucks
- Inventory behind the front row is less accessible
Best For: Warehouses with medium SKU variety and consistent order volume.
Comparing Racking Systems at a Glance
System Type | Access Type | Storage Density | Cost Level | Best Use Case |
---|---|---|---|---|
Selective | 100% selectivity | Low | Low | General-purpose |
Push-Back | 30–75% | High | Medium | High-volume, LIFO |
Drive-In | 25–80% | Very High | Low | Bulk, LIFO |
Cantilever | 100% selectivity | Variable | Medium | Long loads |
Pallet Flow | 100% FIFO | High | High | FIFO inventory |
Double Deep | 50% | Medium-High | Medium | Mid-velocity products |
The following five steps helps warehouse leaders make informed, performance-driven decisions when investing in racking systems:
- Define Inventory Types – Classify by dimensions & weight, product turnover, perishability, and rotation needs to optimize storage retrieval and minimize waste.
- Assess Handling Equipment – Match rack design to forklift type, aisle requirements, and lift height to ensure safe, efficient operation.
- Analyze Throughput Levels – Align inbound/outbound flow, SKU velocity, and order complexity with the right access strategy to boost labor productivity.
- Project Growth Scenarios – Plan for SKU expansion, seasonal spikes, and vertical growth to avoid costly retrofits and support seamless scaling.
- Simulate Layouts – Stress-test pallet flow, clearance, and pick rates in a virtual environment to uncover bottlenecks and improve ROI.
Conclusion
No single racking system universally ranks as the most efficient; efficiency emerges when rack design complements space, labor, equipment, and data systems. Context defines functionality—bulk environments favor high-density solutions, while dynamic order operations demand selectivity and flexibility. Contact our Team of warehouse experts , Align your choice with your warehouse’s unique operational profile to achieve true optimization.
Do you need more information?
Our team of experts will be happy to help you with any questions you may have.
More information